[av_one_full first min_height=” vertical_alignment=” space=” custom_margin=” margin=’0px’ padding=’0px’ border=” border_color=” radius=’0px’ background_color=” src=” background_position=’top left’ background_repeat=’no-repeat’ animation=”]
[av_textblock size=’25’ font_color=” color=”]
Goliath Fall 2016
[/av_textblock]
[av_hr class=’invisible’ height=’-50′ shadow=’no-shadow’ position=’center’ custom_border=’av-border-thin’ custom_width=’50px’ custom_border_color=” custom_margin_top=’30px’ custom_margin_bottom=’30px’ icon_select=’yes’ custom_icon_color=” icon=’ue808′ font=’entypo-fontello’]
[av_textblock size=’25’ font_color=” color=”]
Experiment to Determine Torque to Weight Ratio
[/av_textblock]
[/av_one_full]
[av_hr class=’invisible’ height=’-60′ shadow=’no-shadow’ position=’center’ custom_border=’av-border-thin’ custom_width=’50px’ custom_border_color=” custom_margin_top=’30px’ custom_margin_bottom=’30px’ icon_select=’yes’ custom_icon_color=” icon=’ue808′ font=’entypo-fontello’]
[av_textblock size=” font_color=’custom’ color=’#bfbfbf’]
By: Sou Thao (Electronics and Control Engineer)
Approved by Kristen Oduca (Project Manager)
[/av_textblock]
[av_one_full first min_height=” vertical_alignment=” space=” custom_margin=” margin=’0px’ padding=’0px’ border=” border_color=” radius=’0px’ background_color=” src=” background_position=’top left’ background_repeat=’no-repeat’ animation=”]
[av_heading tag=’h2′ padding=’10’ heading=’Introduction’ color=’custom-color-heading’ style=” custom_font=’#ff6a00′ size=” subheading_active=” subheading_size=’15’ custom_class=”][/av_heading]
[av_textblock size=” font_color=” color=”]
In order to select the correct motor torque to use, an experiment was performed with the previous Goliath to determine the torque to weight ratio for tracked vehicles. From this ratio, we will be able to get an estimate of the amount of torque necessary to drive our new Goliath tank. In order to conduct this experiment we used the following items: the previous semester’s Goliath tank, a weight scale, a breadboard, and an Arduino Leonardo connected with a L293D Motor Driver.
[/av_textblock]
[av_heading tag=’h2′ padding=’10’ heading=’Experiment ‘ color=’custom-color-heading’ style=” custom_font=’#ff6a00′ size=” subheading_active=” subheading_size=’15’ custom_class=”][/av_heading]
[av_textblock size=” font_color=” color=”]
The pin input from the motor driver was connected to the Leonardo digital pins and its output was connected to the motors. This is shown in the Fritzing Diagram in Figure 1.
[/av_textblock]
[av_hr class=’invisible’ height=’20’ shadow=’no-shadow’ position=’center’ custom_border=’av-border-thin’ custom_width=’50px’ custom_border_color=” custom_margin_top=’30px’ custom_margin_bottom=’30px’ icon_select=’yes’ custom_icon_color=” icon=’ue808′ font=’entypo-fontello’]
[av_textblock size=” font_color=” color=”]

[/av_textblock]
[av_hr class=’invisible’ height=’20’ shadow=’no-shadow’ position=’center’ custom_border=’av-border-thin’ custom_width=’50px’ custom_border_color=” custom_margin_top=’30px’ custom_margin_bottom=’30px’ icon_select=’yes’ custom_icon_color=” icon=’ue808′ font=’entypo-fontello’]
[av_textblock size=” font_color=” color=”]
A simple code was created to allow the Goliath to move forward. After this, a measurement of its weight was taken to determine the amount of torque being outputted from each wheels. The weight of the Goliath with the battery pack, a breadboard, and the Leonardo came out to be 442g as shown in Figure 2.
[/av_textblock]
[av_hr class=’invisible’ height=’20’ shadow=’no-shadow’ position=’center’ custom_border=’av-border-thin’ custom_width=’50px’ custom_border_color=” custom_margin_top=’30px’ custom_margin_bottom=’30px’ icon_select=’yes’ custom_icon_color=” icon=’ue808′ font=’entypo-fontello’]
[av_textblock size=” font_color=” color=”]

[/av_textblock]
[av_hr class=’invisible’ height=’20’ shadow=’no-shadow’ position=’center’ custom_border=’av-border-thin’ custom_width=’50px’ custom_border_color=” custom_margin_top=’30px’ custom_margin_bottom=’30px’ icon_select=’yes’ custom_icon_color=” icon=’ue808′ font=’entypo-fontello’]
[av_textblock size=” font_color=” color=”]
Next, we measured the time it took for Goliath to travel a distance of 3ft to determine its velocity as shown in Figure 3.
[/av_textblock]
[av_hr class=’invisible’ height=’20’ shadow=’no-shadow’ position=’center’ custom_border=’av-border-thin’ custom_width=’50px’ custom_border_color=” custom_margin_top=’30px’ custom_margin_bottom=’30px’ icon_select=’yes’ custom_icon_color=” icon=’ue808′ font=’entypo-fontello’]
[av_textblock size=” font_color=” color=”]

[/av_textblock]
[av_hr class=’invisible’ height=’20’ shadow=’no-shadow’ position=’center’ custom_border=’av-border-thin’ custom_width=’50px’ custom_border_color=” custom_margin_top=’30px’ custom_margin_bottom=’30px’ icon_select=’yes’ custom_icon_color=” icon=’ue808′ font=’entypo-fontello’]
[av_textblock size=” font_color=” color=”]
To calculate the torque, we also need the force acting on each wheel and the radius of the wheel. The force acting on the wheel is gravity, and the radius of the wheel is about 20mm or 0.02m. Thus, we used different equations to find our torque as shown in Figure 4:
[/av_textblock]
[av_hr class=’invisible’ height=’20’ shadow=’no-shadow’ position=’center’ custom_border=’av-border-thin’ custom_width=’50px’ custom_border_color=” custom_margin_top=’30px’ custom_margin_bottom=’30px’ icon_select=’yes’ custom_icon_color=” icon=’ue808′ font=’entypo-fontello’]
[av_textblock size=” font_color=” color=”]
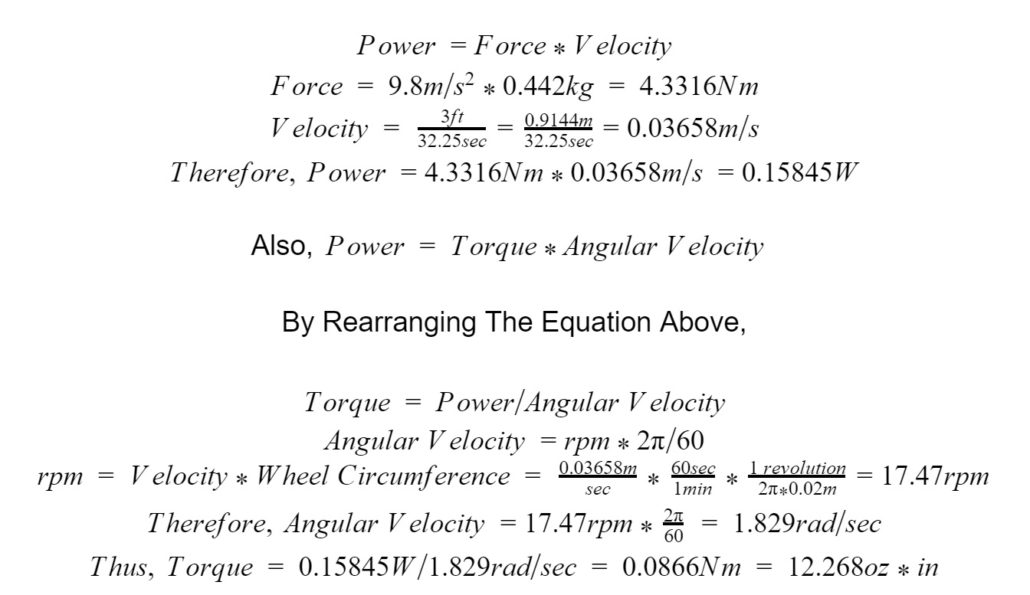
[/av_textblock]
[av_hr class=’invisible’ height=’20’ shadow=’no-shadow’ position=’center’ custom_border=’av-border-thin’ custom_width=’50px’ custom_border_color=” custom_margin_top=’30px’ custom_margin_bottom=’30px’ icon_select=’yes’ custom_icon_color=” icon=’ue808′ font=’entypo-fontello’]
[av_textblock size=” font_color=” color=”]
Now that the torque was determined from the previous Goliath, we can get a torque to weight ratio and determine the amount of torque needed to drive our new Goliath. By dividing the torque by the weight of the previous Goliath, we get 0.0278oz*in/g. This torque ratio can be applied to tracked vehicles, thus, we can get an estimate of the torque we need. Because the estimated weight of the new Goliath is 329g, we multiply this weight by the torque to weight ratio to get our needed torque, which is 9.15oz*in.
[/av_textblock]
[av_heading tag=’h2′ padding=’10’ heading=’Conclusion’ color=’custom-color-heading’ style=” custom_font=’#ff6a00′ size=” subheading_active=” subheading_size=’15’ custom_class=”][/av_heading]
[av_textblock size=” font_color=” color=”]
The minimum size torque we should look for when selecting a motor is 9.15oz*in. We conducted this experiment to determine the torque to weight ratio of the previous Goliath to give us an ideal torque to use for our application. Because Goliath is a tracked vehicle, we could not theoretically calculate the torque in the limited amount of time given because there are many forces acting on the Goliath such as tractive and friction forces. Therefore, by running a test on the previous Goliath, we were able to quickly get a ideal torque so we can select our motors.
[/av_textblock]
[av_hr class=’invisible’ height=’20’ shadow=’no-shadow’ position=’center’ custom_border=’av-border-thin’ custom_width=’50px’ custom_border_color=” custom_margin_top=’30px’ custom_margin_bottom=’30px’ icon_select=’yes’ custom_icon_color=” icon=’ue808′ font=’entypo-fontello’]
[av_textblock size=” font_color=’custom’ color=’#ff6a00′]
Source Material
- https://www.physicsforums.com/threads/calculate-wheel-torque-based-on-known-weight-wheel-size-acceleration-data.288570/
- http://physics.stackexchange.com/questions/52306/calculation-of-torque-for-motor-used-in-4-wheel-robot
- https://www.physicsforums.com/threads/torque-on-a-wheel.779906/
[/av_textblock]
[/av_one_full]