[av_one_full first min_height=” vertical_alignment=” space=” custom_margin=” margin=’0px’ padding=’0px’ border=” border_color=” radius=’0px’ background_color=” src=” background_position=’top left’ background_repeat=’no-repeat’ animation=”]
[av_textblock size=’35’ font_color=” color=” av-medium-font-size=” av-small-font-size=” av-mini-font-size=” admin_preview_bg=”]
Limbi/Spring ’19
[/av_textblock]
[av_hr class=’default’ height=’50’ shadow=’no-shadow’ position=’center’ custom_border=’av-border-thin’ custom_width=’50px’ custom_border_color=” custom_margin_top=’30px’ custom_margin_bottom=’30px’ icon_select=’yes’ custom_icon_color=” icon=’ue808′ font=’entypo-fontello’ admin_preview_bg=”]
[av_heading tag=’h1′ padding=’10’ heading=’Press Fit’ color=” style=” custom_font=” size=” subheading_active=” subheading_size=’15’ custom_class=” admin_preview_bg=” av-desktop-hide=” av-medium-hide=” av-small-hide=” av-mini-hide=” av-medium-font-size-title=” av-small-font-size-title=” av-mini-font-size-title=” av-medium-font-size=” av-small-font-size=” av-mini-font-size=”][/av_heading]
[av_textblock size=” font_color=’custom’ color=’#bfbfbf’ av-medium-font-size=” av-small-font-size=” av-mini-font-size=” admin_preview_bg=”]
Author/s: Samonte, Ridel A. PM and D&M
[/av_textblock]
[av_hr class=’short’ height=’50’ shadow=’no-shadow’ position=’left’ custom_border=’av-border-thin’ custom_width=’50px’ custom_border_color=” custom_margin_top=’30px’ custom_margin_bottom=’30px’ icon_select=’yes’ custom_icon_color=” icon=’ue808′ font=’entypo-fontello’ admin_preview_bg=”]
[av_textblock size=” font_color=” color=”]
[/av_textblock]
[av_textblock size=” font_color=” color=” av-medium-font-size=” av-small-font-size=” av-mini-font-size=” admin_preview_bg=”]
To reduce the use of adhesive and hardware such as nuts, bolts, screws and washers, our D&M team decided to implement the idea of press fitting in our assembly. Press fit is a mechanical fastening between two parts which is achieved by friction after the parts pushed together.
Limbi’s D&M team designed and printed test prototype for our press fit parts to be used in our brace design and docking mechanism layers.
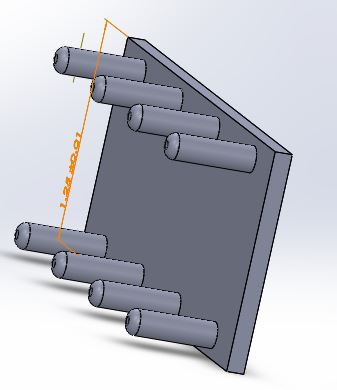
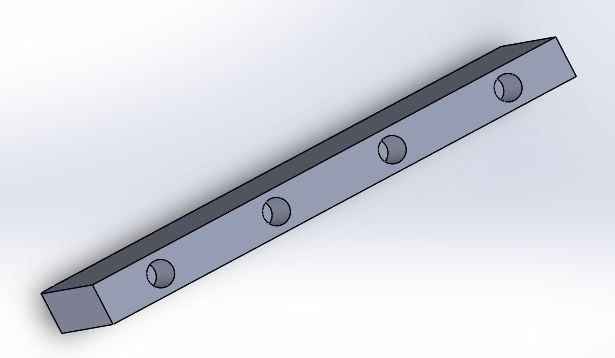
We tested three different extrude and hole pairs:
*length of extrusion and cut are the same: 0.5 inches
- 0.15 in diameter extrusion and 0.16 in diameter cut (0.01 inch difference in diameter).
- 0.15 in diameter extrusion and 0.175 in diameter cut (0.025 inch difference in diameter).
- 0.15 in diameter extrusion and 0.2 in diameter cut (0.05 inch difference in diameter).
Results:
-0.01 in difference is too tight extruded parts would not even fit in the holes.
For he two other extrusion and cut pairs, gravity test is performed: mated parts are held upside down where the friction is the only force holding the male part.
-0.05 in difference is loose which cause the part to fall off.
-0.025 in difference is just the right fit that held the male part from falling during the gravity test. Also, it still allows for the pair to detach.
[/av_textblock]
[av_heading tag=’h1′ padding=’10’ heading=’Implementation to the Limbi Design’ color=” style=” custom_font=” size=” subheading_active=” subheading_size=’15’ custom_class=” admin_preview_bg=” av-desktop-hide=” av-medium-hide=” av-small-hide=” av-mini-hide=” av-medium-font-size-title=” av-small-font-size-title=” av-mini-font-size-title=” av-medium-font-size=” av-small-font-size=” av-mini-font-size=”]
Stuff we will put here woohoo…
[/av_heading]
[av_textblock size=” font_color=” color=” av-medium-font-size=” av-small-font-size=” av-mini-font-size=” admin_preview_bg=”]
We used press fittings in two subassemblies: the two layer for our docking mechanism and the arm braces.
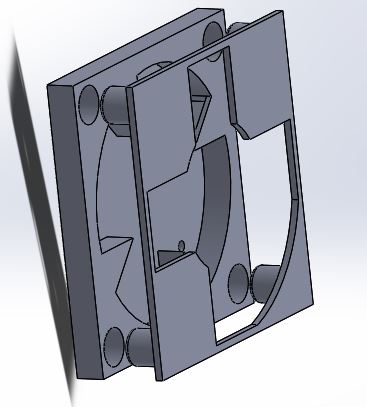
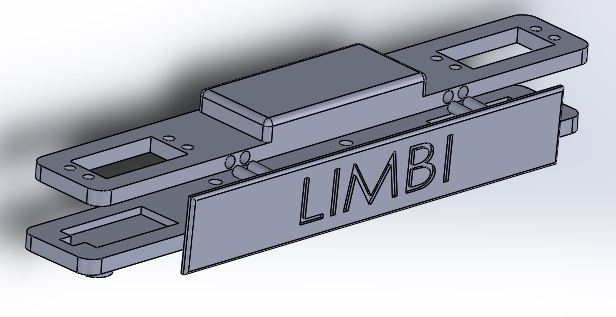
[/av_textblock]
[/av_one_full]