By Ashlee Chang (E&C)
Updated: 03/30/16
Fulfilling Requirements
Level 2 requirements #7 is stated as follows:
7. For the Velociraptor to perform dynamic walking servos moving at a speed of 0.101 sec/10° shall be implemented to the chassis and thus meet the Project Level 1, requirement 5.
The servos will be the motor responsible for the walking and movement of the velociraptor in static walking, dynamic walking, turning, and walking up an incline. Below are the trade-off studies conducted, analyses on the best option, and the team’s final decision.
Servos Introduction
A servo is a handy device in robotics that converts electrical energy to mechanical energy. The device contains a two wire DC motor, a gear train, a potentiometer, an integrated circuit, and an output shaft. There are usually three wires attached to this device: a ground wire (which is usually black), an input voltage wire (which is usually red), and a control wire (which is usually yellow). Using the control wire, a coded signal is transmitted to the servo, which instructs the shaft to rotate to a specific angular position. The potentiometer can be thought of a variable resistor; its role in the servo is to monitor the angle of the shaft. If the shaft is not oriented at the correct angle, it will turn the motor to correct the direction. If the shaft is oriented at the correct angle, it will shut the motor off. A normal servo usually has the capability of positioning between the range of 0* and 180*.
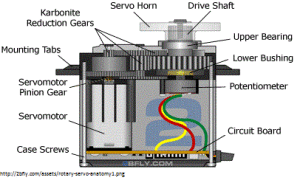
Anatomy of a servo
The velociraptor will need eight servos: two for the head, two for the tail, and two for each leg. The two each on the head and tail will be for balancing purposes; left and right movements will be for balancing as each foot takes a step. The two per leg will be for not only walking, but a turning mechanism as well.
Calculations
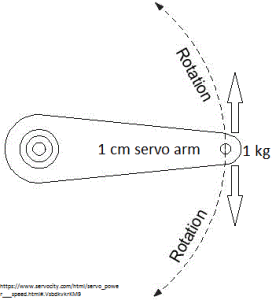
Calculating servo torque
Torque is basically a “twisting force” and is measured in kg*cm. The larger this specification, the more force the servo can exert. If a servo has a power rating of 1 kg*cm, the maximum amount of power it will be able to apply with a 1 cm arm will be 1 kg.
In application to the velociraptor, an estimation for total weight must be made in order to justify the purchase of the servo. For the MicroBiPed, the servo power rating was 3.5 kg*cm at 6.0 V. Thus, for an arm of 1 cm, the servo would be able to produce a 3.5 kg push or pull force to the right angle of the servo arm before stalling. Due to the torque dependency on arm length, the joints of the velociraptor should be kept close to the body to maximize force capabilities. Below is the Titrus III legs showing the arm lengths.
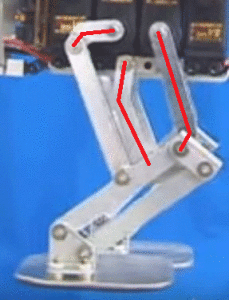
Titrus III arm lengths
The first prototype of the servo has a front arm length of 5.2 cm and back arm length of 2.0 cm. Using these numbers, calculations are made in the “Update” section of this blog post to calculate exactly how much weight each arm alone can handle. The Titrus III is credited and can be seen in action here: https://www.youtube.com/watch?v=GxVv4WNlXMA.
Trade-off Studies
In order to better assess the appropriate servo to use for the velociraptor, a comparison chart was made below of servos in the marketplace.
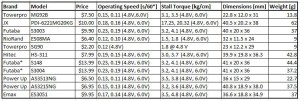
Servos comparison table
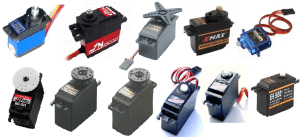
All servos, as per order in the comparison table
* The difference between the two Futaba servos is one has a bearing type of dual bronze brushings, and the latter has a signal ball bearing system.
The first listed servo is the one used by last semester, and the second is one with a lot of torque but Dr. Hill suggested not to go with. 11 different servos were compared, listing some of the most important characteristics. The velociraptor will need eight, so it is important to keep the cost of individual servos at a minimum. The operating speed shows how long it takes for the servo shaft to rotate 60*. It can be seen from the table that all operating speeds are relatively close in value, thus it will not be a major deciding factor. The stall torque is also an important parameter, which shows how much force is needed to move the shaft over a certain distance. In the case of a heavy velociraptor, the stall torque becomes a very important parameter as more torque is needed. The dimensions will affect how large the body encasing them will be. This information is important to M&D division for the size and shape of the body. Lastly, the weight is also significant, considering there are many servos to be accounted for.
Observing the MicroBiPed, weight was undoubtedly the biggest problem. The choice of material used to construct the shell of the robot, PLA, made the overall “micro” robot very heavy as a result. The torque of the servos was not sufficient enough to power through the weight of the MicroBiPed. Thus, it is important that the velociraptor team is weight-conscious in selecting not only the material used to construct the shell, but also the individual component pieces. Below is a table comparing the stall torque to weight ratio of each component. Also below is the price to torque ratio.
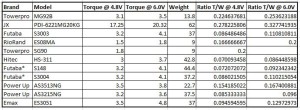
Stall Torque/Weight Ratios
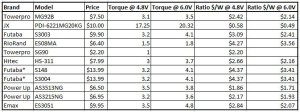
Price/Weight Ratios
Links to all the products:
[Towerpro MG92B] http://www.headsuphobby.com/Towerpro-14g-MG92B-Digital-Metal-Gear-High-Torque-SubMicro-Servo-A-537.htm
[JX PDI-6221MG20KG] http://www.banggood.com/4X-JX-PDI-6221MG-20KG-Large-Torque-Digital-Coreless-Servo-For-RC-Model-p-1031156.html
[Futaba S3003] http://www3.towerhobbies.com/cgi-bin/WTI0001P?I=LXH288&P=8
[RioRand ES08MA] http://www.riorand.com/toys-hobbies/helicopters/riorandr-es08ma-9g-mini-metal-gear-servo-upgrade-mg90s-for-trex-align-450-rc-helicopter-e.html
[TowerPro SG90] http://www.amazon.com/J-Deal%C2%AE-TowerPro-Helicopter-Airplane-Controls/dp/B00X7CJZWM/ref=sr_1_1?ie=UTF8&qid=1455438532&sr=8-1&keywords=servos
[Hitec HS-311] http://www.headsuphobby.com/Hitec-43g-HS-311-Standard-Servo-B-560.htm?categoryId=-1
[Futaba S148] https://www.servocity.com/html/s148_standard_precision.html#.VsBN_fkrKM-
[Futaba S3004] https://www.servocity.com/html/s3004_standard_ball_bearing.html#.VsBOBPkrKM-
[Power Up AS3513NG] http://www.headsuphobby.com/Power-Up-25g-AS3513NG-Analog-Mini-Servo-W-350.htm?categoryId=-1
[Power Up AS3125NG] http://www.headsuphobby.com/Power-Up-38g-AS3215NG-Analog-Standard-Servo-W-400.htm?categoryId=-1
[Emax ES3051] http://www.headsuphobby.com/Emax-43g-ES3051-Digital-Standard-Servo-G-651.htm?categoryId=
Arduino Application
The servo library can be found on the Arduino website, which supports up to 12 different motors on most boards and up to 48 on the Arduino Mega. The Mega can handle up to 12 servos while the Mini can only handle 6-7, so the Mega might be in this semester’s project’s best interest. Two example codes are listed on the Arduino servo website for controlling the position of a servo with a potentiometer and for sweeping the shaft of the servo motor back and forth.
There are three different output types: analog voltage, PWM, and serial. Servo motors use the communication type of PWM (post width modulation). The length of a pulse in seconds will determine how many degrees the motor will turn, and in turn, dictates the angle of the output shaft.
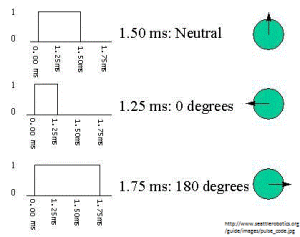
Pulse duration’s relationship to shaft angle
Conclusion
Seeing as the velociraptor will require eight servos, it’s important to minimize weight as much as possible. The servo choice of the MicroBiPed provides the largest torque to weight ratio compared to all other options listed in the table. It’s even more notable that the dimensions are the smallest as well, which will keep the velociraptors body containing most of the servos sizable. To maximize the power ratings of the servos, the arm lengths should also be designed short.
Update (03/14/16)
After the systems and test engineer estimated the project to be around 350 g, torque calculations were able to be made to see exactly how much weight a single servo can handle. The front and back legs (“arm” joints) of the first prototype are 5.2 cm and 2.0 cm, respectively. Using the torque of the TowerPro MG92B servo at 3.5 kg*cm, it is calculated that the front servo alone can handle a weight of approximately 675 g and 1750 g, respectively. This is a basic calculation; of course there are other things to take into consideration like weight distribution of the velociraptor and the fact that some servos work together at the same time. However, this calculation shows that if a single servo can handle the weight of the entire project, then more than one servo (some working together simultaneously) definitely has enough torque to handle the project and then some. The total weight of the project, as estimated by the S&T engineer, is around 500 g. Thus, the TowerPro MG92B was the chosen servo for the velociraptor. All eight servos together come to a total of $60. This servo, also used by last semester’s MicroBiPed, also has the best torque-to-price and torque-to-weight ratio.
Works Cited
[1] What is a servo?
https://www.servocity.com/html/what_is_a_servo_.html#.VsAzEvkrKM8
[2] What’s a servo?
http://www.seattlerobotics.org/guide/servos.html
[3] How to Arduino #3 – Servos
youtube.com/watch?v=ybV8vitYAWU
[4] Servo Power & Speed
https://www.servocity.com/html/servo_power___speed.html#.VsBO9vkrKM8
[5] Understanding RC Servos: Digital, Analog, Coreless, Brushless
http://www.rchelicopterfun.com/rc-servos.html
[6] Servo library
https://www.arduino.cc/en/reference/servo
[7] Titrus III
youtube.com/watch?v=GxVv4WNlXMA