Sojourner/Spring/2019
Sojourner Modifications and Assembly
Author: Connor Hearn
Table of Contents
Introduction
The SolidWorks model of the Sojourner that we used was obtained from Jeff Gomes. He suggested that it should be printed out of carbon fiber ABS, nylon, and Cheetah. However, the project had to be printed out of polycarbonate ABS, nylon, and Ninjaflex, due to accuracy and availability. The initial nylon parts did not fit well and a lot of post-processing needed to be done to get them to work. Though Jeff Gomes’ design is perfect, some changes needed to be made in order for it to be compatible with our items that were used.
Modifications
There were a few modifications that were made to the Sojourner to fit what our group wanted to do with the project.
The phone spring, that kept the cell phone in place within the cell phone tray, was meant to fit the dimensions of an iPhone 4s. The design of the phone spring had to be changed in SolidWorks to be able to fit an iPhone 7.
The original design of the Sojourner would have made the wires from the solar panels to go through the side of the solar panel and cell phone tray. Then, the wires would have to be connected to the micro USB cable which would have to be led around the side of the body, to plug into the back of the body where the 3Dot micro USB port is located. Instead, a hole was drilled through the bottom of the solar panel and cell phone tray. The solar panel wires would go through the solar panel tray and would connect to the diode and micro USB cable in the space under the new phone spring, inside the cell phone tray. The micro USB would go through the cell phone tray and have a direct path to the micro USB port on the 3Dot.
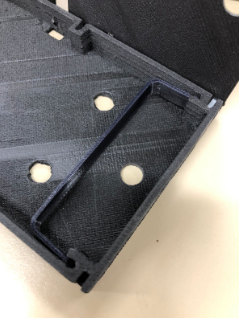
Figure 4. The hole in the phone tray where the micro USB can go though to connect to the 3Dot board.
Lastly, the servo mounts had to be modified to fit the servos that were purchased for the project. The original servo mounts were too small for our servos which prevented our servos from being secured. Because the servos were not secured, the servos did not connect well with the gears that turned the front and back wheels. An extruded cut was made to the mounts to be able to fit the servos. Additionally, another cut had to be made, where the servo mounts connect to the rocker leg. The lip on the original model was too close the the part that connected with the rocker leg, which cause the lip and connector to merge and create a flat surface which rendered the connector useless. An extruded cut was made to cut off the lip to allow for a defined connector.
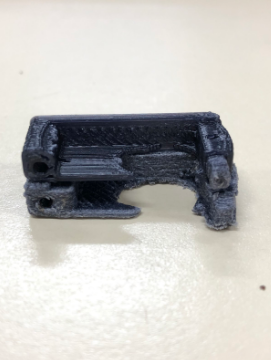
Figure 5. The updated servo mount is on top and the original is on the bottom. It shows how more space was made to fit the servos being used.
Assembly
The Sojourner was assembled based off of Jeff Gomes’ Solidworks model. The gears, shafts, and bushings were printed out of nylon. Nylon works well for gears, however, it is hard to print and replicate. Most of our initial nylon parts had many imperfections which made the parts not fit well together. To fix this, a lot of post-processing needed to be done to get the parts working. The parts can be sanded down or a reaming tool can be used to make parts fit together better. However, nylon is a very difficult material to sand and can take many hours. The original servo gears were printed with a support layer on the bottom, which could have merged parts of the gear teeth together making them less defined. So, the servo gears were reprinted without the supports and came out well.
Conclusion
The SolidWorks model of the Sojourner, obtained from Jeff Gomes, helped immensely and was nearly perfect for our group. However, due to the products available to our group, some modifications had to be made for us to use it, and only apply to the specific products we had at our disposal. The modifications for the phone spring and servo mounts were done in SolidWorks, but the modifications to the cell phone and solar panel trays were not, so that can be done in the future. The assembly of the Sojourner was very time consuming because there were a lot of imperfections in the 3D printed parts. This could be because of the material used or the location used to print. In the end, the more important parts were reprinted and came out to be very accurate.